Metal samples are often considered to be one of the easiest sample types to measure using XRF, but an incorrectly prepared surface can have a huge impact on the quality of the measured data. The quality of the sample preparation will impact every aspect of the analysis, from the calibration through to analysis of unknown materials.
To obtain accurate, precise data with metal samples, you must have a clean, flat surface. Unfortunately, flat is a relative term, and the answer is not as straight forward as one might expect. The quick answer is that the surface should be as smooth as possible.
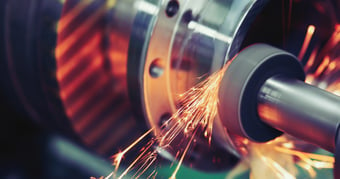
The analysis depth for XRF is dependent on the analyte. Low atomic number elements with long x-ray wavelengths (i.e. light elements), will be easily absorbed by other elements in the matrix, meaning the analysis depth for these light elements is much closer to the surface of the sample than heavier elements with shorter wavelength x-rays. In terms of surface finish, this means that the rougher your surface is, the more it will affect the results for the light elements. Conversely, the smoother your surface finish is, the better the relative count rate will be for the lightest elements being analyzed.
Imperfections in the surface can cause a shadow effect, where elements that are excited on the surface by the incoming x-ray beam, are then subsequently absorbed by a higher region on the surface before they can be detected.(See figure below)
The optimum technique for finishing a given sample will depend on many things, including the type of metal, the hardness and the analytes of interest. Some alloys such as stainless, can easily be re-surfaced with simple alumina grinding paper on a disk grinder such as the HK200, and then finished with diamond polishing if light elements are being evaluated. Others metals such as Co or Ni alloys are harder and will require a more vigorous approach such as a lathe to obtain the optimum finish. Soft alloys such as Cu, Au, Al, or Pb will tend to smear during grinding, and require finishing with a lathe to prevent smearing the softer metal(s) over the harder ones, skewing results for all components. Brittle materials, such as cast iron will be difficult to grind with a disk grinder, and will do best with a pendulum style grinder such as the HK150EX.
One other aspect to consider when preparing your metal samples is contamination. Grinding and polishing media can leave residue on the surface, so considerations must be made for how to deal with this transferred material. Whether its carbon, aluminum, or even lubricating oils. A rinse with alcohol will remove most contamination, or, if you are not looking for the contaminant in your metal, you can ignore any contribution from it. Ultimately, a balance must be found between the time and materials required to obtain the “perfect” finish, and the true requirements of the analysis. Polishing to a mirror finish on every sample is great in theory, but if you are only looking for Fe, Ni and Cr in Stainless, you will not gain any analytical benefit from the extra steps. If on the other hand, you are doing C in steel, the mirror finish will be crucial to obtaining good quality data.
Finally, after the optimum finish has been decided, the standard and sample MUST be finished in the same way. If they are not, all of the careful planning put into determining how to prepare the samples will be useless, as you cannot accurately compare materials that are not finished identically.
For more information on ARMI|MBH sample preparation equipment, click below.